Wednesday, July 02, 2008
What Engineer Simplicity does
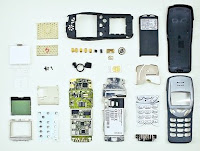
- Initial engineering report
This is a short report which gives everyone some preliminary ideas to work from. I like to start with this as it is a small investment in testing the idea, and provides a lot of information for the path forward.
- Detailed investigation
The initial report or specification has already identified the options, now all the options are investigated in detail. This entails reading datasheets and application notes, speaking to distributors, and really understanding whether the available options will provide the required solution.
- Development of proof of concept
There are two ways to go here, either develop a proof of concept using evaluation boards, or dive straight into the custom hardware design – which is better depends on the risks involved. The risks are a function of the project and the amount of experience with similar designs. Wherever possible it is nicest to speed things up, but a detailed proof of concept can take a lot of risk out of the later stages.
- Final concept
After a full proof of concept it is quite clear how all the pieces fit together. At this stage we should have system block diagrams, communication protocols, component choices, disposal planning and a whole lot more down on paper. The framework for our creation is in place, now we need to make a real prototype.
- Schematic layout
All the concepts and ideas have to be put down into technical drawings (an electronic drawing is called a schematic). Once this is done we have a schematic, a BOM (bill of materials), and other technical files needed for the next steps.
- Printed circuit board layout
The schematic output is used to generate a printed circuit board (PCB layout). The physical size is determined and the components are placed and connected together with tracks. Any mechanical design which is required (e.g. a casing) is also done along side with this step so that the PCB will fit nicely. This can be a time consuming step, as a lot of checking is required, such as tolerances, spacing and component patterns. A set of gerber files are generated which are used to manufacture the actual PCBs.
- Component procurement
Before a prototype can be built, you need all the components that will be placed on the PCB. This step is really happening in parallel with all the other steps to ensure that everything arrives at the right time. Electronic component lead times can vary significantly (from 1 to 16 weeks or more), so a fair amount of planning and scheduling is required.
- Prototype manufacturing
A PCB manufacturer (such as WHCircuit or Trax) makes the PCB's according to the gerber files. The PCB is then populated with the components either by hand or machine. For a first prototype I like to populate the board by hand (where possible) so that I can test each part of the system as I build it up.
- Development and debugging
The amount of effort that goes into making a system work properly is really quite big, but depends on the complexity of the system and the amount of detail that went into all the proceeding steps. It must be shown that each block of the system works and that it all works together properly. Firmware (software that runs on the system) must be tested and developed to a fully functional level. Any bugs that are detected need to be resolved and noted for the future.
- Testing
Once all the functionality is working it must be fully tested, both to check that it is working correctly and to also stress the system to find out if any real world events could break things. Careful attention must be paid to test as many usage cases as possible, and more. Certain countries require specific certifications and any required tests must be done to ensure all the necessary specifications are met.
- Design refinements
All of the testing and development will either have proved that the design works exactly as desired, or indicated areas that need to be improved before going ahead with manufacturing. Steps 4 to 11 are repeated until the product meets the requirement.
- Initial production run
Manufacturing can bring its own challenges to the product from solderability through to the programming and testing of the product. To avoid major manufacturing disasters it is normally better to have a small initial run to iron out any problems in the process.
- Product manufacturing
Once all the manufacturing issues have been resolved it is time to go into full production. This can be a big investment and the quality of the work that has gone before will determine how successful the product is.
- Continuous improvements
There are always things to improve. Wherever possible I try to build in mechanisms that allow easy upgrading of products (such as in–field upgrading of firmware), but it is sometimes necessary to go through some redesign to meet a new requirement or fix a manufacturing issue. Once a product is out in the field you start to get a feel for how it is really used, which teaches you a lot about how to improve the quality.
If you are interested in creating electronic products, then please contact me.
Photo courtesty of Johannes Henseler and licensed under a Creative Commons license.
2 comments :
If you are leaving a comment with your Name and URL then make sure you put http:// in front of your URL for a correct link. You can use some HTML tags such as <a>, <b> and <i> in your comment. Thanks for your message - I appreciate it :)
Note: only a member of this blog may post a comment.
Search This Blog
Subscribe
Tags
About this blog
I'm Duncan Drennan and this blog is about spreading ideas regarding engineering, our environment and creating a better world. You can also follow me on Google Reader.
About Engineer Simplicity
Engineer Simplicity specialises in the design and development of electronic products.
Copyright Notice
Popular Posts
-
As engineers we spend a lot of time solving problems. A customer has a problem and it needs to be fixed. The electronic boards you have just...
-
The short version (my "elevator pitch"): Compact fluorescent lamps (CFLs) use about a fifth of the energy of a normal (incandescen...
-
We are in the middle of an energy crisis and each of us need to make some dramatic changes to ensure that we have electricity, and that the ...
-
eWaste is a particularly difficult issue to deal with as it contains many different materials and lots of extremely hazardous substances. I...
-
So here we are, the first blog post...well, really, here I am. My name is Duncan Drennan and this is my blog on business, design, electronic...
-
There are a lot of steps to turn an idea into a product. Each step requires care and attention to ensure that the best product is created. B...
-
When James Bond used miniature cameras in the 60's and 70's the thought of a wireless phone that can take pictures and send them t...
-
On 29 June 2009 my wife and I became parents to Grace Drennan. It is a great privilege, honour and responsibility to be a part of this amazi...
-
With 48 post over nearly three years, I am certainly not a prolific blog writer. My goal has never been to write a lot, but to rather explor...
-
Urban agriculture (UA) – the production of food within a city – is an important aspect of securing our food supply as well as restoring our...
© The Art of Engineering 2013 . Powered by Bootstrap , Blogger templates and RWD Testing Tool
Hi Duncan
ReplyDeleteI would like to know what your take is on EMC testing and certification, an important part of most electronic development, especially if you ever plan to ship products to other countries. The design part should already be covered, but there is also the step involved for interaction with certification bodies and some extra costs to development.
Other kinds of certification also comes into play when your product will be used in certain environments, eg. automotive (see also here), aviation, and power distribution.
There is also an impotant step for larger scale production to test for product quality, which consists of HALT and HASS tests.
I've noticed that you don't have a step for disposal planning (when the product physically expires and the customer wants to dispose of it). This is something for which I feel we as engineers should take more responsibility, but which is mostly neglected.
Certification is a part of just about any product. It really forms a part of the base design. In a broader sense it falls under "Testing" as a product must comply with the regulations of the country it will be sold into to actually meet the design requirements. It at least deserves a mention in the post, so I will update - thanks for pointing it out.
ReplyDeleteDisposal planning is an interesting one - where does it fit in? The only way that I think disposal can only work correctly is if it is inherently built into the design, so it has to go right up there with the final concept.